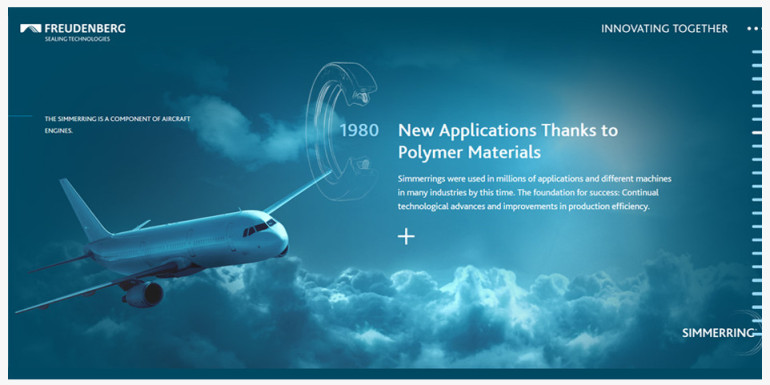
The History of Rotary Shaft Seals: When, Who, and Why?
The Rotary Shaft Seal, also known as the Radial Oil Seal, was first developed in 1929 by the German engineer Walther Simmering. Working for the Freudenberg Group, which remains a leader in the production of seals and technical materials to this day, Simmering's invention revolutionized sealing technology. His goal was to improve the sealing performance of rotary shafts, particularly in industrial and automotive machines where preventing oil leaks and protecting against contamination were critical.
What are Rotary Shaft Seals, and What Do They Do?
Rotary Shaft Seals (Radial Oil Seals) are essential components in industrial, automotive, and other machinery that involve rotating parts. Their primary function is to prevent fluid leaks, such as oils, lubricants, and hydraulic fluids, while also protecting the mechanisms from the ingress of contaminants like dust, water, and chemicals.
What Materials Are Rotary Shaft Seals Made From?
Rotary Shaft Seals are manufactured from a variety of materials, depending on the working environment, the type of fluids being sealed, temperature, and rotational speed. Below are the main materials used:
-
NBR (Nitrile Butadiene Rubber) – A popular material known for its high resistance to oils, greases, and gasoline, as well as moderate temperature resistance (up to 100°C). Commonly used in industrial and automotive applications.
-
FKM (Fluoro Rubber, also known as Viton) – Highly resistant to chemicals, synthetic oils, high temperatures (up to 200°C), fuels, and aggressive media. It is ideal for extreme environments, such as the chemical, aerospace, and energy industries.
-
EPDM (Ethylene Propylene Diene Monomer) – Known for its good resistance to high temperatures, ozone, steam, and various chemicals. Suitable for applications where the seal comes into contact with water, acids, or alkaline solutions.
-
PU (Polyurethane) – Extremely resistant to wear, making it ideal for heavily used equipment where the seal must withstand high mechanical loads.
-
Silicone (VMQ) – A flexible material that is resistant to very low (-50°C) and high temperatures (up to 180°C). It is used in applications requiring a wide temperature range, though it is less resistant to oils and chemicals compared to NBR or FKM.
-
PTFE (Teflon) – A material with very high resistance to chemicals, wear, and high temperatures. It is often used in high-speed rotary applications and aggressive environments.
-
HNBR (Hydrogenated Nitrile Butadiene Rubber) – More resistant to high temperatures and oxidation compared to standard NBR. It is used where greater durability of the seal is required.
-
ACM (Acrylic Rubber) – Resistant to high temperatures (up to 150°C), fuels, and oils, but not resistant to low temperatures and aromatic hydrocarbons. It is commonly used in automotive engines.
Types of Rotary Shaft Seals and Their Construction
Rotary Shaft Seals (Radial Shaft Seals) differ not only in materials but also in their construction, which influences their sealing properties. Here are the main types:
-
A (SC) – Single Lip Shaft Seal Without Tension Spring
Consists of a single sealing lip that contacts the shaft. Used in simple applications with low pressure and contamination levels. The AO type is primarily designed for sealing fluids in environments with minimal contamination. -
AS – Single Lip Shaft Seal with Tension Spring
A more advanced version of type A, equipped with a spring that presses the lip against the shaft. This provides better sealing performance, especially under high-speed and pressure conditions. -
B (BO) – Single Lip Shaft Seal with Metal Housing
This type of seal has a metal frame that strengthens its structure, making it ideal for heavy-duty industrial applications. It offers more mechanical stability than seals with rubber housings. -
TC (AO-TC) – Double Lip Shaft Seal with Dust Lip
Equipped with one sealing lip and an additional dust lip to protect against contaminants entering the sealed mechanism. This is one of the most commonly used types, ideal for industrial and automotive machinery. -
BASL (Double Lip) – Reinforced Double Lip Shaft Seal
Used in harsh conditions where both sealing and protection against contaminants are crucial. BASL seals provide long-term protection and can withstand high mechanical loads and chemicals. -
DUO – Double Lip Seal with Opposite Facing Lips
This special design enables sealing fluids in both directions, making it ideal for hydraulic systems and applications requiring dual sealing protection. -
Cassette Seals
Advanced multi-element seals containing several sealing elements in one housing. Typically, they include a built-in bearing and are used in applications with high contamination and fluid leakage requirements, such as off-road vehicles and agricultural machinery. -
PTFE Shaft Seals (Teflon Seals)
Characterized by high resistance to chemicals, wear, and high temperatures. PTFE seals are used in high-speed rotating applications and in harsh environments where other materials may wear out quickly. -
Low Friction Seals
These seals have special coatings or are made from materials that minimize friction between the shaft and the seal. They are used in applications where minimizing energy loss and increasing energy efficiency is crucial.
Why Use Different Types of Rotary Shaft Seals?
The variety of Rotary Shaft Seals (Radial Shaft Seals) is necessary due to different working conditions, such as:
- Pressure: Some seals are reinforced to withstand higher pressures.
- Temperature: The choice of material depends on the working temperature, ranging from standard conditions to extreme temperatures in the aerospace or chemical industries.
- Working Environment: Seals are tailored to work in dry, wet, chemical, or dusty environments.
Conclusion
Rotary Shaft Seals (Radial Oil Seals) are integral components in many mechanical devices, especially where rotating shafts and components are present. Their primary function is to provide effective sealing—both to prevent oil and grease leakage and to protect against the entry of contaminants. Choosing the right type of seal depends on various factors, such as the type of fluid, temperature range, rotational speed, and working conditions.
The variety of materials (e.g., NBR, FKM, PTFE) and constructions (single-lip, double-lip, with or without a metal frame) allow Rotary Shaft Seals to be adapted to the most demanding applications—from standard industrial use to extreme conditions in the chemical, automotive, or aerospace sectors.
Proper maintenance and regular inspections of seals can significantly extend the life of machinery and improve its performance. Understanding the specific requirements of an application and selecting the appropriate Rotary Shaft Seal are critical to ensuring the reliability and longevity of the equipment.
Leave a Reply Cancel Reply