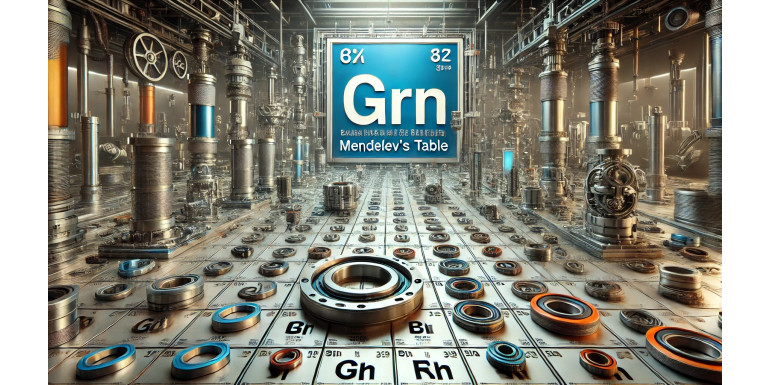
How to Choose the Right Seal Material for Specific Industrial Applications: A Comprehensive Guide for Engineers
Seals play a crucial role in industrial systems by preventing fluid leakage, maintaining pressure, and protecting equipment from contaminants. Choosing the correct seal material is key to ensuring reliable performance, durability, and longevity in a wide range of industrial applications. This guide provides an in-depth look at how to select the right material based on the specific requirements of your industrial processes.
1. Understanding Seal Functionality
Seals are used in various types of equipment, such as pumps, engines, compressors, and hydraulic systems, to create a barrier between two surfaces, preventing the ingress of contaminants and the leakage of fluids. The choice of seal material directly affects the system’s ability to perform under varying pressures, temperatures, and chemical exposures. Misaligned material selection can lead to premature seal failure, increased downtime, and higher maintenance costs.
2. Factors to Consider When Choosing a Seal Material
a. Chemical Compatibility
The chemical environment in which the seal operates is one of the most critical factors in material selection. Exposure to aggressive chemicals, oils, solvents, and gases can degrade seals, causing them to fail prematurely. Engineers must ensure that the material chosen is chemically compatible with the substances it will contact.
-
NBR (Nitrile Butadiene Rubber): Known for its excellent resistance to petroleum-based oils, fuels, water, and various chemicals, NBR is one of the most commonly used materials in hydraulic systems and engines.
-
FKM (Fluoroelastomer, Viton®): Offers superior chemical resistance, particularly to acids, oils, fuels, and solvents, making it suitable for applications in the chemical processing, aerospace, and automotive industries.
-
EPDM (Ethylene Propylene Diene Monomer): This material is resistant to hot water, steam, and various chemicals like alcohols and glycols, making it ideal for applications in food processing and pharmaceutical industries.
b. Temperature Range
Operating temperatures greatly influence the performance of a seal. Materials must be able to withstand both the maximum and minimum temperatures without losing elasticity, cracking, or becoming brittle.
-
Silicone (MVQ): Silicone is known for its flexibility and excellent resistance to extreme temperatures, ranging from -60°C to +230°C. It is widely used in applications requiring high thermal stability, such as in food processing, electronics, and aerospace industries.
-
PTFE (Polytetrafluoroethylene, Teflon®): PTFE can endure temperatures as high as 260°C and offers exceptional chemical resistance. Its low friction properties make it suitable for dynamic sealing applications like in compressors, pumps, and valves.
-
ACM (Acrylic Rubber): Best suited for automotive applications, ACM offers excellent resistance to heat and oil, with a temperature range of -30°C to +150°C, making it ideal for engine gaskets and transmission seals.
c. Pressure and Load Bearing
High-pressure applications require seals that can withstand extreme force without deforming or breaking down. Engineers need to consider both the static and dynamic loads on the seal.
-
PU (Polyurethane): This material provides excellent mechanical strength and is highly resistant to wear, making it suitable for high-pressure hydraulic applications such as hydraulic cylinders and actuators.
-
HNBR (Hydrogenated Nitrile Rubber): Offers superior resistance to both high pressure and high temperature, with added durability against wear and tear. It is often used in oil drilling, gas exploration, and high-performance automotive engines.
d. Wear and Friction Resistance
In dynamic sealing applications, where there is movement between surfaces, friction and wear resistance are critical to extending the life of the seal. Materials must maintain low friction properties to reduce energy loss and prevent overheating.
-
PTFE (Teflon®): Known for its excellent friction-reducing properties, PTFE is often used in seals for rotating equipment like pumps and valves, where frictional wear can be a major concern.
-
FPM (Fluoroelastomer): In addition to its chemical resistance, FPM has excellent wear resistance and is used in applications with dynamic sealing requirements, such as fuel injectors and turbochargers.
e. Environmental Resistance
Exposure to environmental factors like UV radiation, ozone, moisture, and various atmospheric conditions can cause materials to degrade over time. Choosing a material that is resistant to such environmental stressors can significantly increase the longevity of the seal.
-
EPDM: This material excels in outdoor environments, offering resistance to ozone, UV light, and weathering. It is widely used in automotive and outdoor industrial applications like sealing gaskets for doors, windows, and electrical enclosures.
-
FKM (Viton®): In addition to its chemical resistance, FKM is highly resistant to weathering, ozone, and UV light, making it suitable for aerospace and automotive applications where environmental exposure is a concern.
3. Material Overview for Specific Applications
Material | Key Properties | Applications |
---|---|---|
NBR | Oil, fuel, and water resistance, moderate temperature | Hydraulic seals, automotive, fuel systems |
FKM (Viton®) | High chemical resistance, high temperature, wear resistance | Aerospace, automotive, chemical processing |
Silicone (MVQ) | Extreme temperature resistance, flexibility | Food processing, medical devices, high-temperature applications |
PTFE | High chemical resistance, low friction, high temperature | Pumps, valves, rotating equipment |
EPDM | Resistance to steam, weather, ozone, and hot water | Outdoor applications, food processing, pharmaceuticals |
PU | High mechanical strength, wear resistance | Hydraulic systems, actuators, heavy machinery |
HNBR | High pressure and temperature resistance, wear resistance | Oil drilling, gas exploration, automotive engines |
4. Conclusion
Choosing the right seal material is a multi-faceted process that involves careful consideration of the operating environment, chemical exposure, temperature range, pressure, and load conditions. By matching the material properties to the specific application, engineers can ensure reliable and long-lasting seal performance, reducing the risk of downtime and maintenance costs.
FAQs
Q1: What seal material is best for high-temperature applications?
A1: FKM (Viton®) and Silicone (MVQ) are the most suitable materials for high-temperature environments, withstanding temperatures up to 230°C.
Q2: Which material offers the best chemical resistance?
A2: PTFE and FKM (Viton®) provide the highest levels of chemical resistance, making them ideal for applications involving aggressive chemicals.
Q3: What is the best material for seals in outdoor applications?
A3: EPDM is highly resistant to UV, ozone, and weathering, making it ideal for outdoor industrial applications.
Leave a Reply Cancel Reply