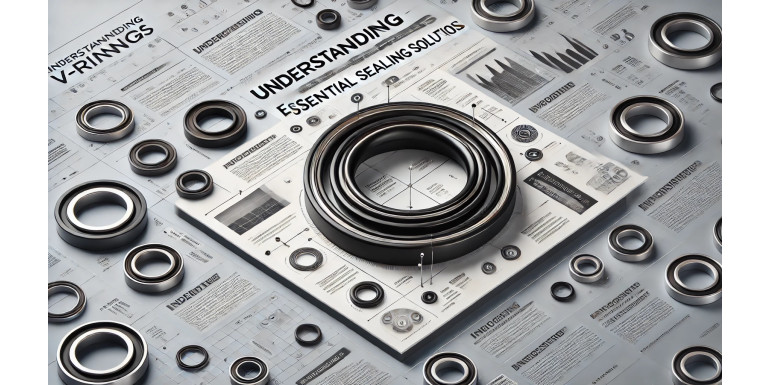
V-Rings: Specialized Sealing Solutions for Industrial Applications
In the world of sealing technologies, V-rings stand out as highly versatile and effective components used across a wide range of industrial applications. Known for their ability to provide reliable sealing in harsh environments, V-rings or V-ring seals are flexible rubber sealing elements used primarily in rotary shafts. Their unique design and functionality make them indispensable for industries where dust, dirt, or liquid contamination could compromise the integrity of mechanical systems.
This article delves into the specific characteristics, advantages, and applications of V-rings, helping you understand why these sealing components are crucial for modern industrial machinery.
What Are V-Rings?
V-rings are axial seals made from elastomers such as Nitrile Butadiene Rubber (NBR) or Viton®. They feature a flexible "V"-shaped lip that acts as a sealing surface, fitting directly onto the rotating shaft. This flexible lip exerts slight pressure on a counterface, typically a bearing or housing, to create a reliable seal that blocks contaminants such as dirt, water, dust, or even oil from entering the machine. The "V" shape also allows the seal to maintain contact under varying conditions of shaft misalignment or thermal expansion, making it highly adaptable to fluctuating operating conditions.
V-rings do not require a tight fit against the shaft, which reduces the overall friction and wear, while still providing an effective seal for the system.
Key Features of V-Rings
-
Simplicity and Flexibility: V-rings are simple in design yet offer great flexibility. Their elastomeric composition allows them to stretch over a range of shaft sizes, and their adaptability to different shaft misalignments makes them particularly useful in environments where exact alignment cannot be guaranteed.
-
Low Friction: Unlike many other sealing systems, V-rings produce minimal friction because they do not have to be installed tightly on the shaft. This reduces energy consumption and ensures a longer lifespan for both the seal and the shaft.
-
Wide Range of Material Options: V-rings are commonly made from NBR or FPM (Viton®) elastomers, which are resistant to a variety of chemicals, oils, and heat. The choice of material allows them to function effectively in temperatures ranging from -40°C to over 200°C, depending on the application.
-
Effective Contaminant Barrier: The primary function of V-ring seals is to protect sensitive components such as bearings, gearboxes, and motors from contaminants. The flexible sealing lip prevents water, dust, dirt, and oil from entering the system, ensuring the longevity and efficiency of the machinery.
-
High-Speed Capability: V-rings can operate efficiently at high rotational speeds, typically up to 12-15 meters per second, without risking damage to the seal or shaft. This makes them suitable for use in industrial fans, electric motors, and other high-speed rotary applications.
How V-Rings Work
The V-ring operates as a contact seal. It is mounted directly onto the shaft and rotates with it, but the flexible lip seals axially against a stationary or counter-rotating surface. The "V" profile allows the lip to bend slightly during rotation, creating the necessary sealing force while keeping friction to a minimum.
As the shaft rotates, the V-ring ensures that contaminants such as dust, water, or grease do not penetrate into the critical parts of the machinery. The elasticity of the V-ring enables it to maintain a consistent seal even as the shaft experiences thermal expansion, misalignment, or vibration.
Applications of V-Ring Seals
Due to their versatility and reliability, V-rings are used across a wide array of industrial sectors. Some of the most common applications include:
-
Electric Motors: In electric motors, V-rings are used to prevent contaminants such as dust, dirt, and moisture from entering the bearings and reducing their lifespan. The low friction of the V-ring seal ensures smooth operation without compromising performance.
-
Pumps and Compressors: In fluid handling systems, such as pumps and compressors, V-rings are effective in sealing rotating shafts, preventing oil or water leakage while simultaneously keeping contaminants from entering the pump’s housing.
-
Industrial Fans: V-rings are ideal for use in industrial fans, where they provide a seal around the shaft, keeping the fan blades free from debris and ensuring the longevity of the bearings.
-
Agricultural and Construction Equipment: Harsh outdoor environments often expose machinery to dust, dirt, and moisture. V-rings provide essential protection for the rotating components in agricultural and construction equipment, preventing the ingress of contaminants.
-
Gearboxes and Transmissions: In gearboxes and transmissions, V-rings help to seal off the rotating shaft while keeping lubricants contained within the system, ensuring smooth operation and minimizing wear.
Types of V-Rings
V-rings come in different models to suit various industrial requirements. The most common types are:
-
VA V-Ring: The VA type is the standard version, used in most general applications. It has a straight back and is designed to seal against the counterface.
-
VS V-Ring: The VS type features a more conical back and is typically used in confined spaces, offering similar sealing properties to the VA type.
-
VL V-Ring: This type has a smaller cross-section, making it suitable for applications where space is limited but where effective sealing is still required.
-
VE V-Ring: The VE type has a wider sealing lip and is designed for applications that require higher protection from contamination.
Material Choices for V-Rings
Selecting the right material for a V-ring seal is critical to its performance, especially in harsh environments. The most common materials are:
-
NBR (Nitrile Butadiene Rubber): NBR is resistant to oils, fuels, and other hydrocarbons, making it suitable for use in engines, gearboxes, and hydraulic systems. It also offers good resistance to wear and tear in general industrial applications.
-
Viton® (FPM): Viton is a fluorocarbon elastomer that is resistant to high temperatures, chemicals, and oils, making it the material of choice for more demanding environments. Viton® V-rings can handle temperatures as high as 200°C and are often used in chemical processing plants or high-performance motors.
-
EPDM (Ethylene Propylene Diene Monomer): EPDM V-rings are resistant to weathering, UV rays, ozone, and water, making them ideal for outdoor applications or in systems exposed to steam or hot water.
Conclusion: Why V-Rings Are Essential for Modern Sealing Solutions
V-rings have proven to be a reliable and versatile sealing solution in a variety of industrial applications. Their simple design, low friction, and effective contaminant protection make them indispensable in ensuring the longevity and performance of rotary equipment. Whether in electric motors, gearboxes, or heavy-duty construction machinery, V-ring seals provide the protection necessary to keep equipment running smoothly and efficiently.
For professionals looking to extend the life of their machinery and reduce maintenance downtime, V-rings offer a cost-effective and highly adaptable solution. Their ability to operate in a variety of environments, from high-speed machinery to dusty construction sites, makes them a vital component in the world of industrial sealing.
For more information and to explore a wide range of V-rings, visit our B2B platform at simmering.pl.
Leave a Reply Cancel Reply