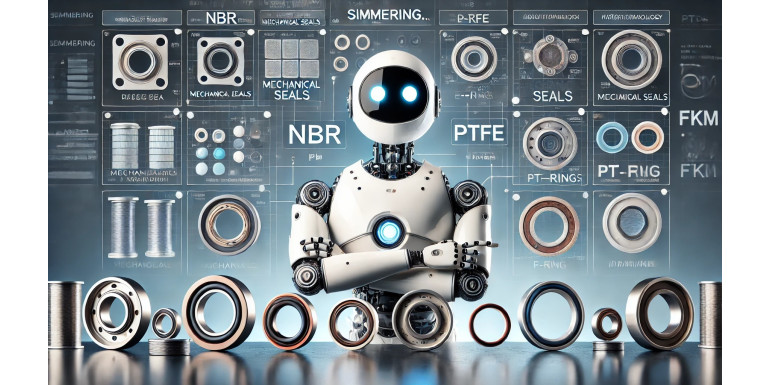
Modern Industrial Seals: How to Choose, Maintain, and Optimize Machine Performance
Introduction
Industrial seals play a critical role in protecting equipment from leaks, contaminants, and excessive wear, directly impacting machine durability and production efficiency. Choosing the right type of seal, selecting suitable materials, and adhering to proper maintenance are essential for maximizing machine performance and longevity. This article provides an in-depth guide on key aspects of industrial seals, including material selection, installation techniques, and advanced sealing technologies.
1. Main Types of Industrial Seals and Their Applications
Various types of seals are used in industrial settings, each designed to meet specific application requirements and environmental conditions. Common seal types include:
-
Mechanical Seals:
Mechanical seals are highly sophisticated and are primarily used in pumps and rotating equipment. They are designed to withstand high pressures and fast movements, making them ideal for high-viscosity fluids like industrial oils. With minimal friction, they enable long-term operation in challenging environments. -
Cassette Seals:
These seals incorporate multi-lip protection systems, making them effective at shielding equipment from mud, dust, and water. They are widely used in agricultural and construction machinery, where exposure to contaminants is unavoidable. The multi-layered design provides an extra barrier, crucial for demanding work conditions. -
O-Rings:
Known for their versatility, O-rings are used in both static and dynamic applications. They come in various materials, such as NBR, FKM, and EPDM, to suit different media and environments. O-rings are commonly employed to seal pipe connections, pumps, tanks, and other industrial components.
Choosing the right seal type depends on the working environment and the media with which the seal will interact. The comprehensive guides on simmering.pl provide detailed descriptions to help you make an informed choice for your application.
2. Key Sealing Materials: Properties and Applications
The choice of sealing material is as crucial as the seal type itself. Each material has unique properties that determine its durability and effectiveness in specific applications:
-
NBR (Nitrile Rubber):
NBR has excellent resistance to oils and greases, making it widely used in automotive and hydraulic industries. It can handle temperatures up to 100°C and resists many industrial fluids, although its resistance to ozone and weather conditions is limited. -
FKM/FPM (Fluoroelastomer):
Known for withstanding temperatures up to 200°C and resisting aggressive chemicals and fuels, FKM is prized in the chemical and automotive industries for its durability in harsh conditions. Its superior chemical resistance makes it ideal for applications that demand long-lasting performance. -
EPDM (Ethylene Propylene Diene Monomer):
EPDM is highly resistant to water, steam, atmospheric conditions, ozone, and various acids and bases. It can operate in temperatures ranging from -50°C to 150°C, making it a preferred choice for water-related applications and outdoor installations. Due to its high chemical resistance, EPDM is also commonly used in the food and pharmaceutical industries. -
PTFE (Teflon):
With a low coefficient of friction and high chemical resistance, PTFE is ideal for applications requiring precision and minimal material wear. It is widely used in the pharmaceutical and food industries as well as in hygienic environments.
For specific applications, it is essential to select the right material based on the medium, temperature, and application characteristics. The material guide on simmering.pl helps match the appropriate seal to operational conditions.
3. Common Seal Installation Mistakes and How to Avoid Them
Proper seal installation is vital for effective performance and longevity. Here are the most common installation errors and tips on avoiding them:
-
Lack of Proper Lubrication:
Dry assembly can damage sealing lips, leading to premature wear. Using the recommended lubricant reduces friction and protects the seal during installation. -
Incorrect Sizing:
Even minor discrepancies in diameter can cause leaks or excessive friction. Precision measurements and appropriate measuring tools are essential to ensure a perfect fit. -
Improper Installation Sequence for Multi-Lip Seals:
For multi-lip seals, each lip must be positioned in the correct direction of media flow. Careful handling during installation is necessary to avoid damage to individual layers.
Correct installation significantly extends seal life, and the "Common Seal Installation Mistakes" guide on simmering.pl offers practical, step-by-step instructions to avoid these pitfalls.
4. Recognizing Signs of Seal Wear and Knowing When to Replace
Industrial seals have a finite lifespan, and wear is inevitable. Ignoring wear indicators can lead to costly failures:
-
Leaks:
Even a minor leak could indicate wear or damage to the sealing lip. Early replacement prevents further issues, such as contaminants entering the machinery. -
Increased Friction or Noise:
Excessive friction may signify seal wear or deformation, often due to improper installation or contamination. -
Presence of Contaminants in the System:
For multi-lip seals, contamination within the system may indicate that the protective lip has worn down and needs replacement.
Regular inspections and timely replacement are essential for maintaining machinery efficiency. The "When to Replace a Seal" article on simmering.pl details signs of seal wear for proactive maintenance.
5. Technological Advancements in Industrial Seals: What You Need to Know
The sealing industry is continually evolving, with new technologies emerging that enhance efficiency and machine life:
-
Advanced Hybrid Elastomers:
Combining elastomers with PTFE and other composites creates seals with increased resistance to extreme temperatures and aggressive chemicals. These hybrid materials are ideal for environments requiring maximum durability. -
Self-Lubricating Seals:
Modern seals with self-lubricating technology incorporate additives that maintain lubrication throughout their lifespan. These seals are particularly beneficial in areas with limited service access. -
Condition-Monitoring Seals:
Seals with built-in sensors to monitor wear are becoming more popular in heavy industries. These sensors alert operators when seal replacement is necessary, enabling maintenance without unplanned downtime.
On simmering.pl, you can find up-to-date information on the latest advancements in seal materials and technologies, making it easier to choose the most efficient solutions for various applications.
Conclusion
Selecting, installing, and maintaining industrial seals is essential for machinery longevity and production efficiency. On simmering.pl, you’ll find a wide range of seals and guides that aid in selecting the right materials and technologies. Advanced solutions, such as hybrid elastomers and condition-monitoring seals, allow for optimized machine performance and increased lifespan, helping you reach new levels of productivity and reliability.
Leave a Reply Cancel Reply