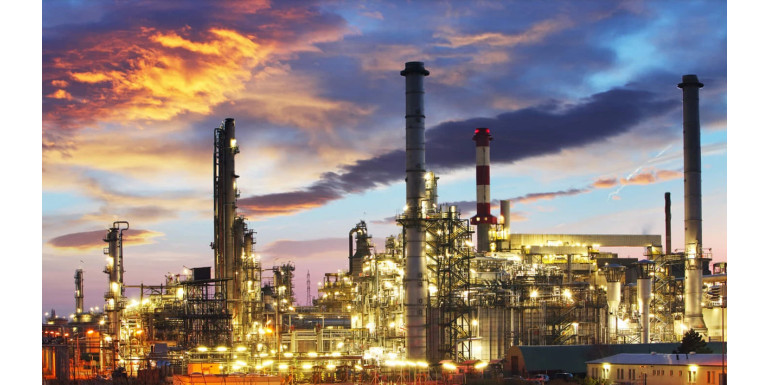
Chemical Resistance of Materials Used in O-Rings and Seals
O-rings and seals play a crucial role in various industries, serving as essential sealing components in systems that frequently come into contact with a wide range of chemicals. The proper selection of elastomer materials, such as EPDM, NBR, HNBR, VMQ, TFE/P, FKM, and FFKM, is vital to ensure long-term sealing efficiency and chemical resistance. Different elastomers offer varying levels of resistance to specific chemicals, making it important to choose the right material based on the application and operating environment.
Chemical Resistance Scale:
- YES – Recommended material, minimal or no deformation when exposed to chemicals.
- Acceptable – Material can be used, but moderate to high deformation may occur.
- NO – Not recommended as the material may degrade or be damaged by the chemical.
Below is a table summarizing the chemical resistance of selected elastomers when exposed to various chemicals:
Chemical | EPDM | NBR | HNBR | VMQ | TFE/P | FKM | FFKM |
---|---|---|---|---|---|---|---|
Acetone | Yes | No | No | Accept | No | No | Yes |
Acetylene | Yes | Yes | Yes | Yes | Yes | Yes | Yes |
Gasoline | No | Yes | - | No | - | Yes | Yes |
Ethanol | Yes | Yes | Yes | Yes | - | Yes | Yes |
Ammonia | Yes | Yes | Yes | Accept | - | No | Yes |
Sodium Nitrate (solution) | Yes | Yes | Yes | Yes | Yes | Yes | Yes |
Bromine | No | No | - | No | - | Yes | Yes |
Freon 12 | Yes | Yes | Yes | Yes | Yes | Yes | Yes |
Kerosene | No | Yes | Yes | No | Yes | Yes | Yes |
Salt Water | Yes | Yes | Yes | Yes | - | Yes | Yes |
Ammonium Hydroxide (concentrated) | Yes | No | - | Yes | - | Yes | Yes |
How to Interpret the Table? This table provides key insights into how different elastomers respond when in contact with common chemicals. For instance, EPDM is particularly resistant to chemicals like acetone, ethanol, and ammonia but should not be used with gasoline or bromine. On the other hand, NBR performs well in applications involving petroleum-based products but is unsuitable for acetone or bromine exposure.
Key Elastomer Materials:
- EPDM (Ethylene Propylene Diene Monomer): Highly resistant to ozone, aging, and environmental factors, but unsuitable for petroleum and hydrocarbon contact.
- NBR (Nitrile Butadiene Rubber): Ideal for sealing applications exposed to oils and fuels, though it lacks resistance to acetone or strong acids.
- HNBR (Hydrogenated Nitrile Butadiene Rubber): An enhanced version of NBR with better heat and ozone resistance, commonly used in the automotive and oil industries.
- VMQ (Silicone Rubber): Flexible at both high and low temperatures, resistant to many chemicals, but not recommended for contact with oils.
- FKM (Fluorocarbon Rubber, Viton): Renowned for its high temperature and chemical resistance, widely used in the aerospace and automotive industries.
- FFKM (Perfluoroelastomer): Offers the highest chemical resistance, suitable for extreme chemical environments where other elastomers fail.
Conclusion: The chemical resistance of materials used in O-rings and seals is essential for ensuring long-lasting sealing performance. Choosing the right elastomer based on the operating environment can greatly impact the effectiveness of the seal and the durability of the machinery. Selecting the appropriate material minimizes the risk of failures and extends the lifespan of equipment.
Keywords: chemical resistance, elastomers, O-rings, seals, NBR, EPDM, FKM, FFKM, industrial seals, sealing performance
Leave a Reply Cancel Reply