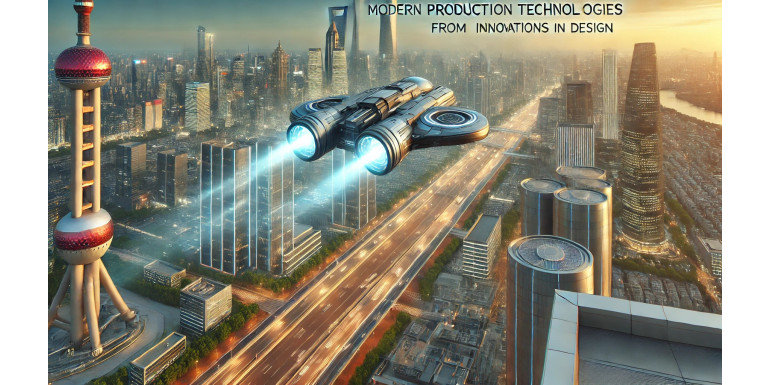
Modern Production Technologies for Simmerings: From Materials to Innovations in Design
The production of technical seals such as simmerings has evolved significantly over the past decades. These advancements have been driven by the need for higher durability, better performance, and adaptability to extreme conditions in industries like automotive, aerospace, and heavy machinery. Simmerings, also known as rotary shaft seals, play a critical role in preventing leakage of lubricants while blocking contaminants like dirt and moisture. The continuous improvement in materials and production processes is pushing the boundaries of what simmerings can achieve in various industrial applications.
In this article, we’ll explore the latest innovations in the production of simmerings, focusing on materials, design, and the most advanced manufacturing technologies. Additionally, we'll touch on the role of global production hubs, particularly in China, where cutting-edge factories produce high-performance simmerings under our GRN brand.
1. Advanced Materials: Moving Beyond Standard Elastomers
The core of a high-quality simmering is the material from which it is made. Traditionally, NBR (Nitrile Butadiene Rubber) has been the most commonly used elastomer for its versatility and balance of cost and performance. However, as industrial requirements become more demanding, manufacturers are turning to more advanced materials. Some of these include:
-
FKM (Fluorocarbon Rubber): Known for its excellent resistance to high temperatures (up to 250°C), chemicals, and oils, FKM is ideal for applications in the automotive and aerospace sectors where seals must withstand harsh environments.
-
HNBR (Hydrogenated Nitrile Butadiene Rubber): HNBR improves upon standard NBR by offering superior resistance to heat, oil, and abrasion, making it perfect for dynamic applications in the oil and gas industries.
-
PTFE (Polytetrafluoroethylene): PTFE-based seals are gaining traction due to their low friction coefficient, which is critical for applications requiring reduced wear and enhanced chemical resistance. PTFE seals can operate in extremely high temperatures and aggressive chemical environments.
-
MVQ (Silicone Rubber): While not as mechanically robust as other materials, silicone seals offer excellent temperature resistance, making them a good fit for food processing and medical applications where high heat sterilization is common.
These materials not only provide superior sealing performance but also help extend the lifespan of machines by minimizing wear on critical components. Additionally, multi-material seals, combining elastomers like PTFE and HNBR, are becoming more prevalent, offering enhanced performance by leveraging the benefits of each material in specific environments.
2. Innovative Design Enhancements for Superior Performance
The design of simmerings has also seen notable innovations in recent years, with manufacturers continually optimizing the geometry of the seal to reduce friction, improve sealing efficiency, and extend operational lifetimes. Some of the most important design developments include:
-
Multi-lip Seals: Traditional simmerings were often single-lip designs, but modern applications, particularly those involving high-speed machinery, benefit from multi-lip configurations. These designs allow for additional layers of protection, ensuring that even if one lip fails, the others maintain the seal, prolonging the component's life.
-
Integrated Dust Lips: To prevent contamination from dust, dirt, and other particulates, many modern simmerings include dust lips as an integral part of the design. This feature is especially useful in off-road machinery, construction equipment, and agricultural applications where exposure to harsh environmental conditions is constant.
-
Reduced Friction Geometry: Recent innovations in seal lip design have led to a reduction in contact friction, which not only decreases wear on the seal but also minimizes energy loss in mechanical systems. Seals with reduced-friction geometries are particularly valuable in applications such as electric vehicles (EVs), where energy efficiency is paramount.
3. State-of-the-Art Production Technologies
The manufacturing of high-performance simmerings relies on cutting-edge production technologies. Today’s factories are highly automated, utilizing advanced processes such as:
-
Injection Molding and Compression Molding: These methods have been optimized for precision and repeatability, ensuring consistent quality across large production volumes. The use of automated molding processes ensures that tolerances are maintained, and defects are minimized.
-
Laser Scanning and Digital Inspection: Quality control is critical in the production of technical seals, and modern factories employ laser scanning and digital inspection systems to verify that each seal meets stringent specifications. These technologies help detect minute defects that could lead to seal failure in the field.
-
Automated Compound Mixing: The perfect blend of elastomers and additives is crucial for high-performance seals. Many factories have adopted automated mixing systems that guarantee a consistent compound quality, essential for ensuring that seals maintain their performance characteristics across different batches.
4. The Role of China’s Modern Factories
China is home to some of the world’s most advanced manufacturing facilities for technical seals, including those under our GRN brand. These state-of-the-art factories utilize the latest technologies in both material processing and automated manufacturing. Not only do these facilities produce large volumes of seals for global distribution, but they are also capable of meeting the stringent quality demands of industries such as automotive, aerospace, and heavy machinery.
At our production hubs in China, we manufacture GRN-brand simmerings that adhere to international standards. These facilities are equipped with cutting-edge machinery for precise molding and high-speed production, ensuring that every seal meets the rigorous quality control standards required by our global customers.
The combination of advanced materials, innovative design, and modern production processes enables us to produce high-performance simmerings that offer reliability and durability in the most demanding industrial environments.
5. Future Outlook: Eco-friendly and High-Performance Seals
As environmental regulations become stricter and industries seek more sustainable solutions, the development of eco-friendly seals is on the rise. Manufacturers are exploring the use of biodegradable materials and sustainable production methods to minimize the environmental impact of seal production.
Additionally, as machinery becomes more advanced, especially in sectors such as electric vehicles and robotics, the demand for seals that can handle high speeds, reduced energy consumption, and extreme environmental conditions will continue to grow. At the forefront of this innovation, companies like TG Ersatzteile Polska, producing GRN seals, will play a key role in providing advanced sealing solutions for the industries of the future.
Conclusion
Modern production technologies for simmerings are transforming the performance, durability, and applicability of these critical components. From the use of advanced materials like PTFE and HNBR to innovations in seal design and automated production processes, the industry is evolving to meet the demands of increasingly complex machinery. With cutting-edge production facilities in China and a commitment to high-quality manufacturing, TG Ersatzteile Polska, through the GRN brand, continues to push the boundaries of what’s possible in the field of technical seals.
Leave a Reply Cancel Reply