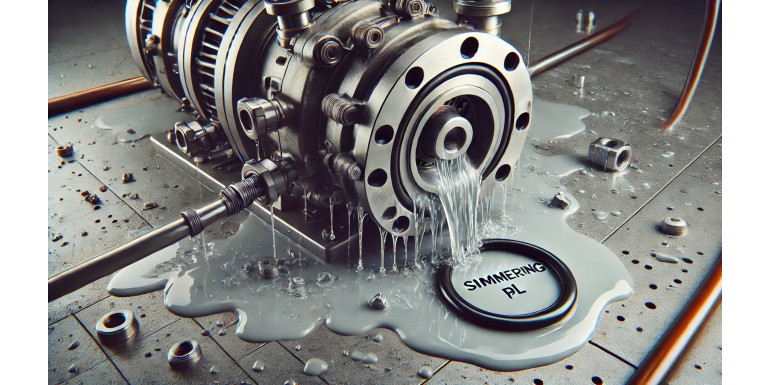
Common Causes of O-Ring Failures in Industrial Applications and How to Prevent Them
O-rings are essential components in sealing applications across many industries, from automotive to aerospace, and hydraulic systems. Their role, though often overlooked, is vital for ensuring the integrity of equipment. However, even the best O-rings can fail if not used or maintained properly. Understanding the common causes of O-ring failure can help prevent costly downtimes, improve the lifespan of machinery, and avoid unnecessary replacements.
Here’s a detailed guide to the most common reasons O-rings fail and how to prevent these issues effectively.
1. Extrusion and Nibbling
What Is It?
Extrusion occurs when an O-ring is pushed out into the clearance gap between two components due to high pressure. This often leads to "nibbling," where the O-ring material tears as it's forced into these gaps during operation.
Causes:
- High pressure exceeding the material’s capacity
- Excessive clearance between components
- Rapid cycling between pressure variations
How to Prevent:
- Use O-rings made from high-pressure-resistant materials like HNBR or PTFE.
- Minimize the clearance between metal parts to prevent excessive movement.
- Add back-up rings to support the O-ring in high-pressure applications, reducing the likelihood of extrusion.
2. Thermal Degradation
What Is It?
Thermal degradation occurs when O-rings are exposed to extreme temperatures, either too high or too low for the material to handle, causing cracking, hardening, or softening.
Causes:
- Operating temperatures beyond the O-ring’s material limit
- Frequent or sudden temperature changes
How to Prevent:
- Choose materials suited to the temperature range of your application. For example, Viton® (FKM) handles high temperatures, while Silicone and EPDM are ideal for low-temperature conditions.
- Avoid sudden temperature spikes that can shock the material and degrade its elasticity.
3. Chemical Attack
What Is It?
Certain chemicals can attack O-ring materials, causing swelling, shrinkage, cracking, or even complete disintegration, particularly in applications involving aggressive fluids or solvents.
Causes:
- Exposure to incompatible chemicals
- Incorrect O-ring material for the type of fluid being sealed
How to Prevent:
- Ensure chemical compatibility by using materials like Viton® (FKM) for chemical exposure, EPDM for water-based fluids, or NBR (Nitrile) for petroleum-based oils.
- Always refer to a chemical compatibility chart when selecting O-rings for industrial applications involving chemicals.
4. Compression Set
What Is It?
Compression set happens when an O-ring becomes permanently deformed after being compressed for a long time, leading to a loss of sealing force. The O-ring fails to recover its original shape once the compressive force is released.
Causes:
- Continuous exposure to high temperatures
- Over-compression during installation
- Using O-rings made from materials not resistant to compression set
How to Prevent:
- Select materials with low compression set characteristics like FKM, HNBR, or Silicone.
- Avoid over-tightening or excessive compression during installation.
- Regularly replace O-rings in high-temperature environments to ensure proper sealing performance.
5. Installation Damage
What Is It?
O-rings can be damaged during installation due to improper handling, including stretching, pinching, or cutting. Scratches or tears in the O-ring surface often lead to early failure.
Causes:
- Incorrect installation techniques
- Use of improper tools
- Insufficient lubrication during assembly
How to Prevent:
- Lubricate the O-ring before installation to reduce friction and avoid damage.
- Use specialized installation tools to prevent stretching or cutting.
- Follow manufacturer guidelines for installation to avoid placing excess stress on the O-ring.
6. Abrasive Wear
What Is It?
Abrasive wear occurs when an O-ring faces constant friction or rubbing against a surface, leading to material loss, pitting, or scoring. This is common in dynamic applications where the O-ring moves with the shaft.
Causes:
- Rough or dirty surfaces in contact with the O-ring
- Inadequate lubrication
- Use of inappropriate materials for dynamic applications
How to Prevent:
- Use wear-resistant materials like Polyurethane or HNBR for dynamic seals.
- Ensure surfaces are clean, smooth, and free from debris before installation.
- Apply the appropriate lubricant to reduce friction.
7. Swelling
What Is It?
Swelling occurs when the O-ring absorbs fluids, causing it to expand. This swelling compromises the O-ring's sealing ability and leads to eventual failure, often by disintegration or extrusion.
Causes:
- Exposure to incompatible chemicals or oils
- Use of incorrect O-ring material for the fluid being sealed
How to Prevent:
- Select a material resistant to the fluids it will be exposed to. NBR is suitable for petroleum-based oils, while EPDM is ideal for water-based fluids.
- Review the chemical composition of the system to ensure the right O-ring material is chosen.
8. Hardening and Cracking
What Is It?
O-rings can harden or crack over time due to prolonged exposure to ozone, sunlight, or high temperatures. This reduces their flexibility, causing them to lose their sealing ability and eventually fail.
Causes:
- Long-term exposure to ozone or UV radiation
- High-temperature environments
- Incompatible materials
How to Prevent:
- Use materials with excellent weathering and ozone resistance like EPDM or Viton® (FKM).
- Avoid storing O-rings in direct sunlight or in environments where they are exposed to ozone-producing equipment.
Conclusion: Choosing the Right O-Ring Material is Key
Understanding the causes of O-ring failures and taking preventive measures is crucial for maximizing the lifespan and reliability of industrial systems. Proper material selection is fundamental — matching the O-ring material to the specific conditions of your application can drastically reduce failures, downtime, and maintenance costs.
At Simmering.pl, we offer a wide range of high-quality O-rings for industrial use, designed to withstand even the most challenging environments. Whether you're working in high-pressure hydraulics, aggressive chemical processes, or temperature-sensitive systems, we have the right sealing solutions for your needs.
FAQ:
1. What is the most durable O-ring material?
2. How often should I replace O-rings in high-temperature environments?
- It’s best to inspect O-rings regularly in high-temperature environments and replace them as soon as you notice signs of wear, such as hardening or cracking.
3. What is the best O-ring material for oil applications?
Keywords:
- O-ring failure causes
- Prevent O-ring failure
- Industrial O-rings
- Abrasion-resistant O-rings
- Chemical-resistant O-rings
- O-ring for high pressure
- Hydraulic O-rings
- Dynamic O-ring seal
By addressing these common failure modes and offering practical solutions, this article provides valuable insight for both engineers and maintenance teams looking to extend the lifespan of their O-ring seals. Proper selection, installation, and maintenance are the keys to avoiding costly failures and ensuring optimal system performance.
Leave a Reply Cancel Reply