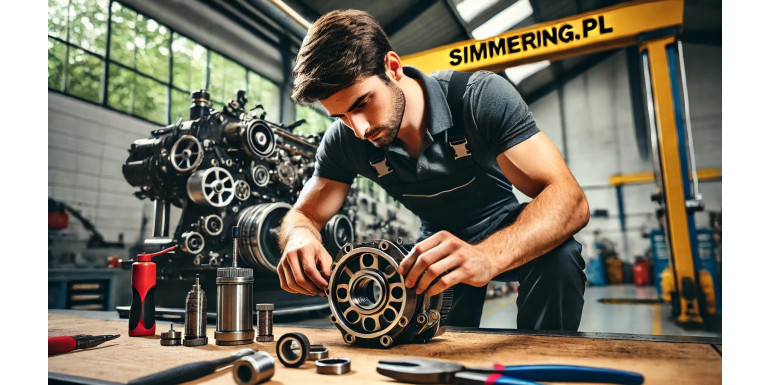
Introduction to Oil Seal Installation: Why Proper Installation is Critical in High-Performance and Industrial Applications
Oil seals, also known as radial shaft seals or simmerrings, play a vital role in protecting mechanical components from oil leaks and preventing contaminants like dust and dirt from entering the system. In high-performance and industrial applications, such as drivetrain systems, differential shafts, and hydraulic machinery, ensuring a proper seal is crucial for maintaining the longevity and efficiency of equipment.
Even the best oil seals, such as those from Corteco, can fail if they are not installed correctly. Improper installation is one of the leading causes of premature seal failure, leading to oil leaks, equipment breakdowns, and costly repairs. In this article, we will discuss why proper installation is essential, common installation mistakes, and how to avoid them to ensure that oil seals provide reliable and long-lasting performance.
Why Proper Installation of Oil Seals is Critical
Oil seals are designed to perform under precise conditions, maintaining a tight barrier to prevent oil from leaking while also keeping contaminants out. However, even minor installation errors can disrupt their effectiveness, leading to:
- Shortened Seal Lifespan: Incorrectly installed seals wear out faster, leading to premature failure and the need for frequent replacements.
- Oil Leaks: Misaligned or improperly fitted seals can cause oil to leak, resulting in loss of lubrication and potential damage to machinery.
- Ingress of Contaminants: Without a proper seal, dirt, dust, and moisture can infiltrate the system, leading to corrosion and damage to internal components.
In high-performance and industrial environments, where machines are subjected to extreme conditions, a compromised seal can cause significant downtime, loss of productivity, and increased maintenance costs.
Common Mistakes During Oil Seal Installation
-
Misaligned Seal (Cocked Seal)
One of the most frequent installation mistakes is the misalignment of the oil seal. Even a slight misalignment, known as a "cocked" seal, can create gaps between the seal and the shaft, leading to uneven wear and oil leakage. Ensuring proper alignment during installation is crucial to prevent these issues -
Improper Surface Preparation
Before installing an oil seal, it is essential to clean and inspect the shaft and bore thoroughly. Contaminants such as dirt, oil residues, or metal shavings can damage the seal during installation and cause premature failure. A clean and smooth surface is critical to ensure a secure fit -
Using the Wrong Tools
Applying too much or too little force during installation can easily damage the seal. Using improper tools can result in scratches, deformities, or incomplete fitting. It's important to use dedicated installation tools that apply even pressure around the seal, ensuring a correct fit without damaging the seal or the shaft -
Selecting the Wrong Material
Using the wrong material for the application environment is a common mistake. NBR (nitrile butadiene rubber) seals are great for standard oil applications but may not withstand extreme heat or chemical exposure. In such cases, FKM (Viton) or other high-performance materials may be required. Ensuring the correct material is chosen based on the operating temperature and fluid exposure is vital for the longevity of the seal -
Failure to Lubricate the Seal
Applying a thin layer of lubricant to the seal lip and the shaft before installation helps reduce friction and makes the installation smoother. Installing the seal "dry" can lead to excessive wear during the first operation and may even cause the seal to tear or fail prematurely.
How to Avoid Common Installation Problems
-
Use the Right Tools: Always use proper installation tools, such as guide sleeves and mandrels, to apply even pressure around the seal. This prevents cocking and ensures that the seal is installed perfectly aligned.
-
Prepare the Surface: Before installation, thoroughly clean and inspect the shaft and bore for contaminants, rough edges, or scratches that could compromise the seal’s performance.
-
Lubricate the Seal: Applying a small amount of compatible lubricant helps the seal slide smoothly into place without damaging the lip. This also ensures a tighter fit once in operation.
-
Select the Correct Material: Match the seal material with the operating conditions. For example, if the seal will be exposed to extreme temperatures or aggressive chemicals, consider using a material like FKM or EPDM instead of NBR.
-
Perform Regular Maintenance: Regular inspections of the seal and shaft can help identify wear or potential issues early. This can prevent major failures and extend the lifespan of the machinery.
Conclusion
Proper installation of oil seals is critical to ensuring their longevity and reliability, particularly in high-performance and industrial applications. Even minor mistakes during installation can lead to significant problems such as oil leaks, premature seal failure, and contamination of the system. By following best practices for installation, using the right tools, and selecting the appropriate material, you can prevent these issues and keep your machinery running smoothly for longer periods.
Investing the time and effort to install oil seals correctly not only improves the performance of your equipment but also reduces downtime, maintenance costs, and the risk of major failures.
Leave a Reply Cancel Reply