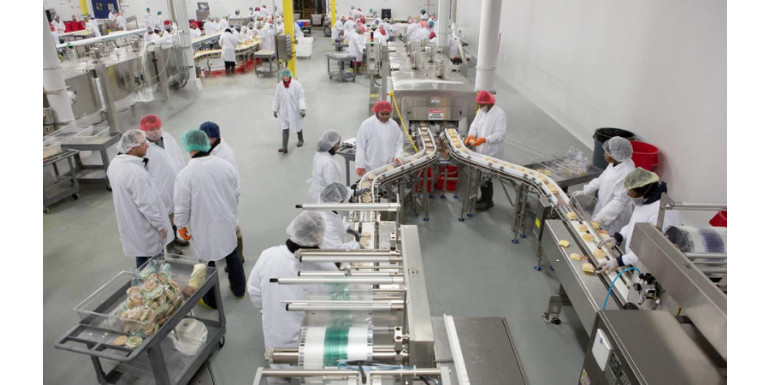
O-Rings in the Food Industry (FDA): Hygienic Requirements, Material Selection, and Applications
The food industry relies heavily on sealing solutions to maintain product safety, quality, and efficiency in processing and packaging. O-rings are essential components in this sector, offering reliable sealing capabilities in a wide range of applications. This article explores the key considerations for selecting O-rings in the food industry, the hygienic standards they must meet, and practical examples of their use.
1. Hygienic Requirements for O-Rings in the Food Industry
Compliance with Regulations:
O-rings used in food processing must adhere to strict international standards to ensure they are safe for use in contact with food. Key regulations include:
- FDA (Food and Drug Administration): Ensures that materials meet food-grade requirements in the United States.
- EU Regulation 1935/2004: Governs materials that come into contact with food in the European Union.
- NSF Standards: Apply to food and water safety globally.
Characteristics of Hygienic O-Rings:
- Non-toxic materials: No harmful substances that could leach into food.
- Resistance to cleaning agents: Ability to withstand frequent cleaning cycles involving hot water, steam, or harsh chemicals.
- Smooth surfaces: Minimize microbial growth and ensure easy cleaning.
2. Material Selection for Food-Grade O-Rings
Choosing the right material is critical to ensure the O-ring meets the demands of the application while adhering to hygiene standards.
Common Materials and Their Properties:
- EPDM (Ethylene Propylene Diene Monomer):
- Excellent resistance to hot water, steam, and cleaning agents.
- Suitable for applications involving acidic and alkaline environments.
- Silicone (VMQ):
- Wide temperature range (-60°C to +200°C).
- Ideal for sealing in low-pressure applications and environments with high-temperature fluctuations.
- FKM (Fluoroelastomer):
- Outstanding resistance to oils, fats, and aggressive chemicals.
- Suitable for sealing applications involving fatty foods.
- PTFE (Polytetrafluoroethylene):
- High chemical resistance and non-stick properties.
- Used in extreme temperature conditions and highly corrosive environments.
3. Applications of O-Rings in the Food Industry
O-rings are employed in various equipment and processes across the food industry. Below are some of their most common applications:
1. Packaging Machines:
- Sealing components in vacuum sealers, heat sealers, and filling machines.
- Ensures a sterile environment for food packaging.
2. Pumps and Valves:
- Critical in systems that transport liquid or semi-liquid food products.
- Prevents leaks and contamination during processing.
3. Processing Equipment:
- Used in mixers, blenders, and grinders to seal shafts and moving parts.
- Withstands mechanical stress and high-temperature cleaning cycles.
4. Dairy and Beverage Industries:
- O-rings are used in milk and juice processing systems.
- Maintain hygiene and prevent spoilage through effective sealing.
4. Maintenance and Replacement of O-Rings
Proper maintenance is essential to ensure the longevity and effectiveness of O-rings in food processing equipment.
Best Practices:
- Regular Inspection:
- Check for wear, cracks, or swelling, which indicate degradation.
- Scheduled Replacement:
- Replace O-rings at recommended intervals to prevent unexpected failures.
- Proper Storage:
- Store in cool, dry places to maintain material integrity.
Impact of Poor Maintenance:
Neglecting O-ring maintenance can lead to contamination, equipment downtime, and loss of product quality.
5. Innovations and Future Trends in Food-Grade O-Rings
Advancements in Materials:
- Development of hybrid materials combining the benefits of different elastomers.
- Increased use of bio-based and eco-friendly materials for sustainability.
Smart O-Rings:
- Integration of sensors to monitor wear and predict failures.
Improved Standards:
- Ongoing updates to international regulations to enhance food safety.
Conclusion
O-rings play a vital role in the food industry by ensuring reliable sealing, maintaining hygiene, and supporting efficient production processes. Understanding the regulatory requirements, material properties, and application-specific needs is crucial for selecting the right O-ring. With advancements in materials and technologies, the future of O-rings in the food industry promises even greater reliability and innovation.
At Simmering.pl, we offer a wide range of food-grade O-rings tailored to meet the needs of the food industry. Contact us today to find the perfect sealing solution for your applications!
Leave a Reply Cancel Reply