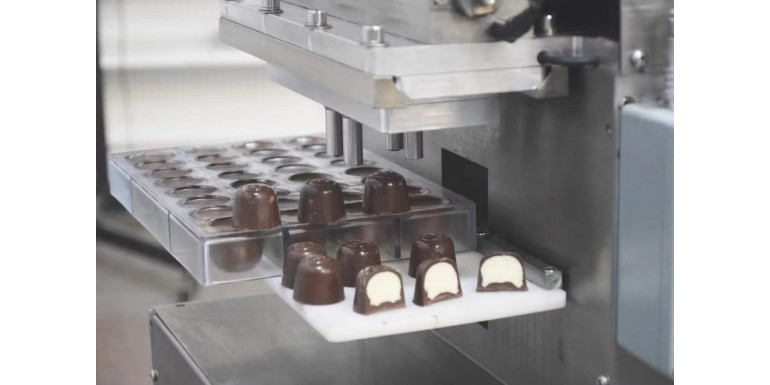
Rotary Shaft Seals in the Food Industry: Ensuring Hygiene and Efficiency
Introduction
Rotary shaft seals, commonly known as simmerings, play a vital role in the food industry by not only enhancing operational efficiency but also ensuring the hygiene and safety of food production processes.
The Importance of Rotary Shaft Seals in the Food Industry
In a sector where hygiene standards are paramount, rotary shaft seals are indispensable for:
- Preventing Leaks: They eliminate the risk of lubricants or oils contaminating food products, safeguarding food quality and safety.
- Blocking Contaminants: By sealing machinery components, they prevent dust, moisture, and other contaminants from entering production systems.
- Maintaining Hygiene: Made from materials compliant with FDA and EU 1935/2004 standards, these seals ensure safe contact with food.
Hygienic Requirements and Standards
Rotary shaft seals used in the food industry must meet strict regulations, such as:
- FDA Certification: Ensures that materials are approved for contact with food by the U.S. Food and Drug Administration.
- EU 1935/2004 Regulation: Establishes European guidelines for materials intended to come into contact with food.
Compliance with these standards guarantees that seals will not compromise the quality or safety of food products.
Materials for Food-Grade Rotary Shaft Seals
The choice of material is crucial to meet the demands of various food production processes. Common materials include:
-
Silicone (MVQ):
- Highly resistant to high temperatures.
- Ideal for bakery and drying equipment.
-
Fluoroelastomer (FKM/Viton):
- Excellent chemical and thermal resistance.
- Suitable for systems cleaned with aggressive agents.
-
NBR (Nitrile Butadiene Rubber):
- Resistant to oils and fats.
- Used in dairy and fat processing machinery.
-
PTFE (Teflon):
- Outstanding resistance to extreme temperatures and chemicals.
- Perfect for sensitive food industry applications.
Applications of Rotary Shaft Seals in the Food Industry
Rotary shaft seals are used in various food production segments, including:
- Processing Machinery: Ensure smooth operation of mixers, grinders, and homogenizers by preventing leaks and contamination.
- Bottling Lines: Protect against moisture and contaminants in filling and capping machines.
- Bakeries: Silicone seals withstand high temperatures in industrial ovens and wafer lines.
- Cooling Systems: Provide reliable performance in low-temperature environments, critical for refrigeration and freezing units.
Challenges and Solutions
The food industry presents several challenges for rotary shaft seals:
- Extreme Temperatures: Seals must endure both high temperatures in baking and low temperatures in freezing systems.
- Aggressive Cleaning Agents: Frequent cleaning cycles demand seals resistant to harsh chemicals.
- Food Contact Compliance: Materials must ensure safe contact without compromising food quality.
Selecting the right materials and seal designs addresses these challenges, ensuring reliable and safe production processes.
Benefits of Using the Right Rotary Shaft Seals
Properly selected rotary shaft seals offer numerous advantages:
- Extended Machine Life: Prevent leaks and contamination, reducing wear and prolonging equipment lifespan.
- Lower Maintenance Costs: Minimized risk of breakdowns translates into reduced operational expenses.
- Enhanced Food Safety: Prevent contamination, ensuring high-quality food products.
Conclusion
Rotary shaft seals are essential components in the food industry, ensuring not only operational efficiency but also hygiene and safety. Choosing the right materials and seal designs is critical to meeting the industry’s strict demands. By doing so, manufacturers can maintain the highest standards of product quality and ensure the reliability of their production processes.
For top-quality rotary shaft seals tailored to the food industry, visit Simmering.pl today!
Leave a Reply Cancel Reply